We have a lot of questions about using our parachutes and other UAV / Drone products in order to get an FAA waiver or international CAA approval for flight over people. We hope this FAQ will help answer many of the questions about ASTM F3322-18 testing standards which the FAA may ask for. This will also address questions regarding the drone, drone weight and how each can affect the waiver process or availability.
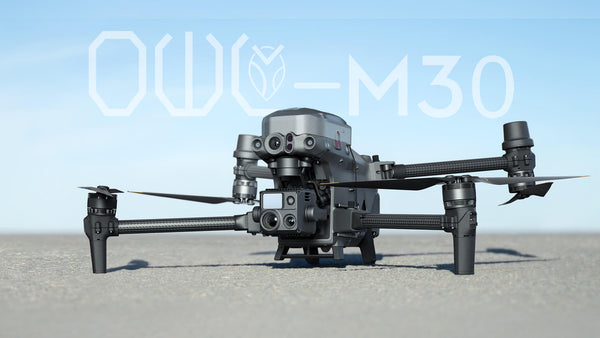
Q - Has Flyfire already tested their parachute recovery systems (PRS) to the ASTM F3322-18 standard?
A – No! The ASTM standard is not just for us as the parachute manufacturer to test and meet the standard. The ASTM standard is designed for testing and certification of the complete system: both the Flyfire PRS and the drone it's used with. It’s this combined solution that is tested to the standard and certified. The certification is not valid with a different combination of PRS, or drone.
Q – Does testing need to be done for each drone and PRS system sold?
A – No. The testing is done using representative samples of the complete system and this is what's tested for certification. Also the testing is done at both minimum and maximum weights and over a range of flight conditions and payload options.
Q – Who does the testing; does the Parachute Manufacturer or Drone Manufacturer do their own testing?
A – Neither. Testing is done at an FAA authorized third party testing authority (TPTA). There are a number of these across the US, mostly associated with the various FAA testing sites. The nearest one to us is in Nevada. Of course, before testing, the drone manufacturer and the parachute manufacturer should have already done their own testing per the standard to be sure to pass the TPTA suite of testing. Testing is expensive.
Q – What information and testing does the ASTM Standard require?
A – It requires:
A tranche of documentation that needs to be provided to the TPTA as called out by the ASTM standard.
Materials and strength information about the PRS is provided by the Parachute Manufacturer. A key factor is strength information about the parachute and whether it is strong enough to not break under any deployment conditions.
Flight testing through a suite of different flight types, failure scenarios, at minimum and maximum weights to cover payload options (cameras, sensors, etc). For multi-copter drones, the minimum number of flights is 45 flights. There are 9 different flight scenarios and failure conditions tested, with 5 tests each. There needs to be 5 successful flights in a row to pass a particular test. If one flight fails, then the five need to be redone.
Q – What is the result of the TPTA?
A – A detailed report written by the TPTA combined with the documentation together with the flight testing results. Key results would include:
All the various documents used for the ASTM certification.
Specifics on the drone tested, with min / max weights, or optional payloads that are tested for.
Specifics on the PRS, parachute size and type, and how it is mounted and any connections to the drone.
Testing will determine the certified minimum flight altitude that is required when flying over people.
Q – After testing, how does one get a waiver?
A – When applying to the FAA for your waiver, they will ask for proof of safety of the drone and PRS. You would then provide the ASTM certification report as proof of the safety of the drone with the PRS.
Q – What features does the PRS need to include for the standard?
A – The PRS must have:
A parachute
Some way to launch or eject the parachute
Harnesses and rigging to connect the parachute to the drone
An Autonomous or Automatic Trigger System (ATS). This device automatically detects a drone failure and ejects the parachute. The OWLis an example of an ATS. Automatic parachute ejection software (parachute channel) in the autopilot cannot be used on it’s own. The ATS must be able to operate independently of the autopilot in case the autopilot fails. The autopilot parachute channel out can be combined into the ATS so both systems can initiate the parachute ejection.
A secondary radio should also be provided so the pilot in command (PIC) can also eject the parachute if needed.
Q – Does the drone have any special requirements to meet the standard?
A – In an ideal world – Yes! The ASTM specification called out these requirements, most all of which are missing on most commercial drones like DJI, or Yuneec:
A place or way to mount the PRS on the drone. For most drones this is relatively easy to work around.
Hard-points where the parachute recovery harness allows connections to the drone. Many times the best hard points are the rotor booms.
Drone's primary power source as an input to the ATS so the voltage can be monitored. Not available in most commercial drones. Easier with open source drones.
Low voltage 5V power source to keep the ATS battery charged and to provide secondary power.
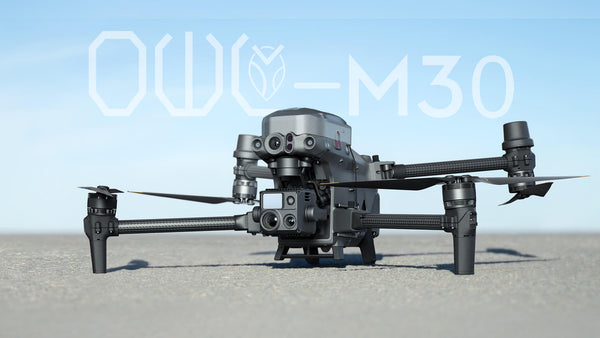
Q - Has Flyfire already tested their parachute recovery systems (PRS) to the ASTM F3322-18 standard?
A – No! The ASTM standard is not just for us as the parachute manufacturer to test and meet the standard. The ASTM standard is designed for testing and certification of the complete system: both the Flyfire PRS and the drone it's used with. It’s this combined solution that is tested to the standard and certified. The certification is not valid with a different combination of PRS, or drone.
Q – Does testing need to be done for each drone and PRS system sold?
A – No. The testing is done using representative samples of the complete system and this is what's tested for certification. Also the testing is done at both minimum and maximum weights and over a range of flight conditions and payload options.
Q – Who does the testing; does the Parachute Manufacturer or Drone Manufacturer do their own testing?
A – Neither. Testing is done at an FAA authorized third party testing authority (TPTA). There are a number of these across the US, mostly associated with the various FAA testing sites. The nearest one to us is in Nevada. Of course, before testing, the drone manufacturer and the parachute manufacturer should have already done their own testing per the standard to be sure to pass the TPTA suite of testing. Testing is expensive.
Q – What information and testing does the ASTM Standard require?
A – It requires:
A tranche of documentation that needs to be provided to the TPTA as called out by the ASTM standard.
Materials and strength information about the PRS is provided by the Parachute Manufacturer. A key factor is strength information about the parachute and whether it is strong enough to not break under any deployment conditions.
Flight testing through a suite of different flight types, failure scenarios, at minimum and maximum weights to cover payload options (cameras, sensors, etc). For multi-copter drones, the minimum number of flights is 45 flights. There are 9 different flight scenarios and failure conditions tested, with 5 tests each. There needs to be 5 successful flights in a row to pass a particular test. If one flight fails, then the five need to be redone.
Q – What is the result of the TPTA?
A – A detailed report written by the TPTA combined with the documentation together with the flight testing results. Key results would include:
All the various documents used for the ASTM certification.
Specifics on the drone tested, with min / max weights, or optional payloads that are tested for.
Specifics on the PRS, parachute size and type, and how it is mounted and any connections to the drone.
Testing will determine the certified minimum flight altitude that is required when flying over people.
Q – After testing, how does one get a waiver?
A – When applying to the FAA for your waiver, they will ask for proof of safety of the drone and PRS. You would then provide the ASTM certification report as proof of the safety of the drone with the PRS.
Q – What features does the PRS need to include for the standard?
A – The PRS must have:
A parachute
Some way to launch or eject the parachute
Harnesses and rigging to connect the parachute to the drone
An Autonomous or Automatic Trigger System (ATS). This device automatically detects a drone failure and ejects the parachute. The OWLis an example of an ATS. Automatic parachute ejection software (parachute channel) in the autopilot cannot be used on it’s own. The ATS must be able to operate independently of the autopilot in case the autopilot fails. The autopilot parachute channel out can be combined into the ATS so both systems can initiate the parachute ejection.
A secondary radio should also be provided so the pilot in command (PIC) can also eject the parachute if needed.
Q – Does the drone have any special requirements to meet the standard?
A – In an ideal world – Yes! The ASTM specification called out these requirements, most all of which are missing on most commercial drones like DJI, or Yuneec:
A place or way to mount the PRS on the drone. For most drones this is relatively easy to work around.
Hard-points where the parachute recovery harness allows connections to the drone. Many times the best hard points are the rotor booms.
Drone's primary power source as an input to the ATS so the voltage can be monitored. Not available in most commercial drones. Easier with open source drones.
Low voltage 5V power source to keep the ATS battery charged and to provide secondary power.